Welding is a versatile and valuable skill that can lead to lucrative career opportunities. Whether you are a seasoned professional or just starting in the field, it’s essential to evaluate the most profitable welding procedures to ensure financial success. In this article, we will analyze various welding techniques and their potential for profitability.
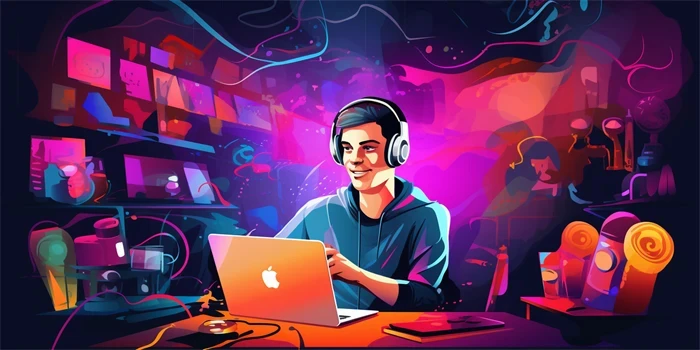
1. TIG Welding: Precision and Profitability
Tungsten Inert Gas (TIG) welding is renowned for its precision and ability to deliver high-quality welds. This procedure requires a steady hand and extensive training, making it ideal for intricate projects such as aerospace components or medical equipment. Due to the specialized skill set it demands, TIG welding often commands higher wages and profitability.
Moreover, TIG welding finds extensive applications in the automotive industry, where customization and precision are valued. Whether it’s modifying exotic car exhaust systems or crafting specialized frames, TIG welding remains a profitable choice.
2. MIG Welding: Efficiency and Affordability
Metal Inert Gas (MIG) welding, also known as Gas Metal Arc Welding (GMAW), offers a balance between efficiency and affordability. It utilizes a consumable electrode wire and a shielding gas to create welds quickly, making it suitable for large-scale projects and rapid production lines.
The relative ease of learning MIG welding also contributes to its profitability. Aspiring welders can quickly acquire the necessary skills and certifications, which opens up numerous job opportunities in industries such as construction, shipbuilding, and manufacturing.
3. Stick Welding: Versatility and Demand
Shielded Metal Arc Welding (SMAW), commonly known as stick welding, is one of the oldest and most versatile welding methods. Its widespread popularity can be attributed to its convenience and ability to perform well in challenging conditions.
Stick welding is often sought after in sectors such as infrastructure development, pipelines, and heavy equipment repair. Its versatility allows for the welding of various metals, making it a profitable choice for welders who work on diverse projects.
4. Flux-Cored Arc Welding: High-Deposition Rates
Flux-Cored Arc Welding (FCAW) offers high-deposition rates and is well-suited for thick materials and structural welding. It is a variation of MIG welding that utilizes a hollow wire filled with flux, eliminating the need for a shielding gas.
Due to its efficiency in welding projects involving heavy-duty materials like steel and stainless steel, FCAW is often in demand in industries such as shipbuilding, oil refineries, and industrial construction. Its effectiveness in high-deposition welding translates into higher profitability for skilled welders.
5. Resistance Spot Welding: Automotive Industry’s Choice
Resistance Spot Welding (RSW) is widely used in the automotive industry to join sheet metal parts. It involves applying pressure and an electric current to create welds without consuming any additional materials.
This welding procedure offers fast cycle times, making it highly efficient for mass production. With the automotive industry continuously expanding, skilled spot welders are in constant demand, ensuring a profitable career path.
6. Laser Welding: Precision at its Peak
Laser welding, a non-contact process that uses a focused laser beam, is renowned for its unmatched precision and minimal heat input. This technique is commonly used in industries where intricate welds are required, such as electronics, jewelry, and fine metalwork.
Although laser welding equipment can be costly, its accuracy and efficiency justify the investment, thereby creating profitable opportunities for welders specializing in this technique.
7. Submerged Arc Welding: Productivity for Heavy Industries
Submerged Arc Welding (SAW) is specifically designed for heavy-duty welding applications. By submerging the arc and weld joint in a flux, it protects the weld pool from contaminants and reduces the release of fumes.
SAW is widely used in industries such as shipbuilding, construction, and structural fabrication, where high productivity and exceptional weld quality are essential. Skilled welders proficient in this technique can expect ample job opportunities and profitability.
8. Robotic Welding: Automation and Efficiency
Robotic welding offers improved efficiency and reduced labor costs through automation. This technology allows for precise and high-speed welding, making it highly sought after in industries with large-scale production lines.
Industries such as automotive manufacturing, aerospace, and heavy equipment fabrication extensively utilize robotic welding systems. Welders with expertise in programming and operating such systems can enjoy excellent job security and profitability.
9. Underwater Welding: Unique Challenges and Rewards
Underwater welding is undoubtedly one of the most challenging and specialized forms of welding. It requires divers and welders to work in an underwater environment, facing unique challenges such as extreme pressures and limited visibility.
However, the scarcity of underwater welders and the niche nature of the profession lead to higher wages and potential for increased profitability. Offshore oil drilling platforms, ship repairs, and bridge construction are among the industries that often require skilled underwater welders.
10. Combination Welding: Expanding Your Skill Set
Combination welding, also known as multi-process welding, involves using multiple welding procedures to achieve optimal results. This versatility allows welders to adapt to a wider range of projects and industries, increasing their marketability and potential profitability.
By combining techniques such as TIG, MIG, and stick welding, professionals can handle different materials, sizes, and welding scenarios. Mastery of multiple welding procedures opens opportunities in construction, manufacturing, and specialized welding services.
Frequently Asked Questions
Q1: Which welding procedure pays the highest?
A1: While wages vary depending on factors such as experience and industry demand, TIG welding is generally considered one of the most lucrative welding procedures due to its precision and demand in specialized fields.
Q2: Can I make a good living as a welder?
A2: Yes, becoming a welder can be financially rewarding, especially when specializing in high-demand welding procedures or industries. Continuous skill development and securing certifications can also contribute to increased earning potential.
Q3: How long does it take to learn welding?
A3: The time required to learn welding varies depending on factors such as the welding procedure and the individual’s dedication and aptitude. While basic proficiency can be attained in a few months, mastering welding techniques and gaining experience often takes several years.
Q4: What safety measures should welders follow?
A4: Welders should prioritize safety by wearing proper protective gear, such as helmets, gloves, and fire-resistant clothing. Adequate ventilation, eye protection, and awareness of potential hazards are also crucial for preventing accidents and maintaining occupational health.
Q5: Can I weld as a side gig or freelance?
A5: Yes, welding can be pursued on a freelance basis or as a side gig. Many welders offer their services to individuals or businesses for specific projects, repairs, or customizations. This flexibility allows welders to supplement their income while catering to their clients’ needs.
References:
1. American Welding Society. (www.aws.org)
2. “The 8 Types of Welding.” Tulsa Welding School. (www.weldingschool.com)
3. Vogel, M., & Bohlmann, M. (2018). Introduction to Welding Technology.